BOBST MASTER DM5 optimizes label production for I.B.E. in Italy

Mex, Switzerland, 14th October 2021
Since investing in the BOBST MASTER DM5, I.B.E. S.r.l. has experienced how the All-Inline, All-in-One label press brings huge benefits to converters and their customers in the widest range of applications.
The MASTER DM5, which features both UV inkjet and flexo technologies, offers priming, printing, lamination, embellishment and converting in a single pass. For the Italian printing house, the modular solution has turned out to be more than just another label press; as well as producing high quality print, it is successfully addressing the challenging space between short and long runs by offering fast setup, high flexibility and cost-effective production.
“For us the biggest advantages of the DM5 are, firstly, that it is very competitive on the medium – and most requested – runs from 2000 to 8000 metres. This means it is bridging a gap which I felt was there before, although to be fair, we are able to embrace all kinds of run lengths with this press,” said CEO Roberto Spreafico. “Secondly, flexibility – you can produce any kind of job required by the market, from the most complex to the simplest label, in a single pass thanks to the versatility of the press and the excellent integration between digital and analogue printing technologies.”
Delivering faster time to market
As part of the Spreafin Group of five companies, which employs over 250 people, I.B.E. was established in 1998 in Merate, in the province of Lecco in northern Italy.
The company produces self-adhesive labels, multi-layers labels and shrink sleeves for a wide variety of customers mainly in the food, wine and oil, household and personal care, and industrial sectors, both in Italy and internationally. Production capabilities include offset, flexo and digital printing technologies with constant investments made in new solutions to keep pace with the fast-moving market.
“The label sector has always been accustomed to short time-to-market demands, maybe because the label is one of the last things you put on the packaging. Speed is therefore key to success in this market,” said Mr Spreafico. “We need fast turnaround capabilities to meet these expectations. Sometimes we deliver labels in just two or three days, and this is where digital technology and automation play a huge role.”
Embellishment and automation for added value
The I.B.E. team first saw the MASTER DM5 in action at Labelexpo Europe in 2019. Impressed with the native resolution of 1200 dpi and running speed of up to 100 m/min, the decision was quickly made to select BOBST.
“The modularity of the press meant that our company was able to install a unique configuration matching our specific needs, while the high degree of automation has contributed to cost, time and waste savings,” said Mr Spreafico.
“A major advantage of the DM5 is the inline embellishment, which adds value without creating a bottleneck in production,” he explained. “We chose to include all kinds of finishing and embellishment options to print high quality labels in one single pass so we can best serve all sectors and industries – for example, the cosmetics and wine label verticals, which require the highest level of embellishment.”
The MASTER DM5 has been designed with automation in mind with each module operated by digital technologies. The success of the press is due to the fact that most of the manual steps usually associated with flexo printing have been automated with BOBST technology, such as DigiFlexo for full digital registration and printing pressure setting. This also takes care of registration between the digital unit and the flexo stations, both before and after digital printing, which means the operator can trust the machine to keep registration and work autonomously. The result is an ultrafast set-up time, exceptionally high press uptime and outstanding repeatability.
“One of the reasons we chose the DM5, in addition to the digital part, relates to the automation in the traditional printing,” said Mr Spreafico. “The flexo groups are well integrated and have automatic register control camera technology on each station. The press is also very easy to operate and features job changes on the fly, non-stop semi-rotary die-cut change and waste matrix system that can make even the most complicated shapes requested by our customers.” He added that the setup times achieved were comparable to those experienced in standalone digital printing, despite the multi-process nature of highly embellished jobs.
Covering all verticals with one press
The breath of the applications that can be produced on the BOBST MASTER DM5 has enabled I.B.E. to move jobs from offset and screen-printing to the All-Inline label press. Mr Spreafico said, “Thanks to the four flexo groups, delam/relam and inline lamination, we can cover all types of verticals without any distinction. This also gives us the opportunity to quickly replicate labels that are usually printed with other technologies, like offset and digital toner or pure flexo.”
The substrates that can be printed on the press include self-adhesive label stock – paper, PET, BOPP and PVC – unsupported paper (min. 80 gsm), light carton up to 180 gsm and, as an option, unsupported filmic material. The company was pleasantly surprised to discover that the press can tackle also wine applications. Mr Spreafico revealed, “For some wine labels printed on less textured papers, we were able to replace offset technology with the DM5.”
Moreover, I.B.E. has found that the durability of the print can compete with screen-printing without the need for lamination, which has saved on plastics, reduced the thickness of the labels, and simplified the finishing process. The inks have a high resistance to abrasion and chemical agents, making them suitable for chemical labels, according to Mr Spreafico.
After few months of usage of the DM5, he concluded, “We have really hit the target with this investment especially as the market continues to request small and medium quantities, low stocks and increasingly frequent orders. These kind of services with a short lead time, combined with the quality and repeatability, are the main benefits that our customers are experiencing.”
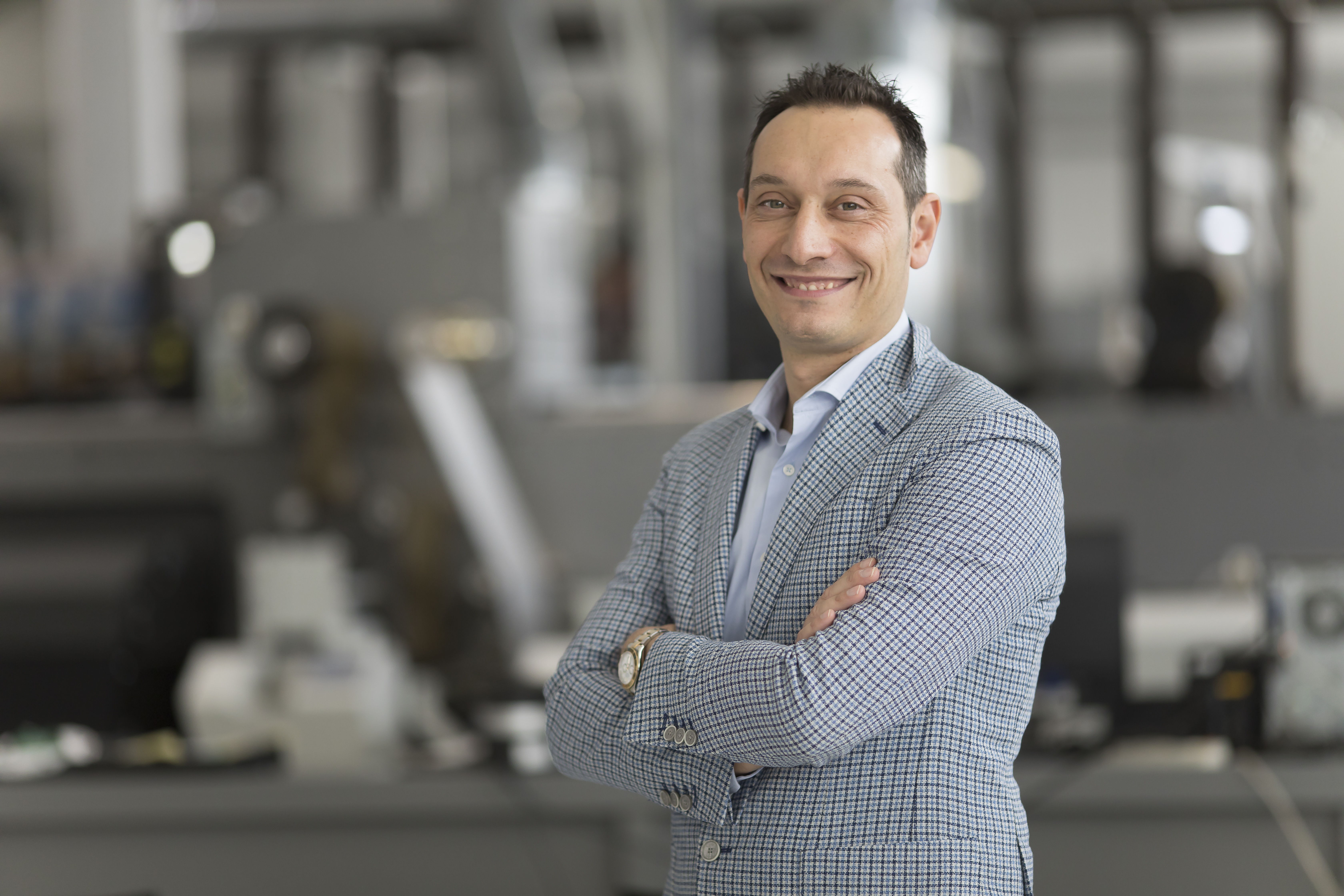
About BOBST
We are one of the world’s leading suppliers of substrate processing, printing and converting equipment and services for the label, flexible packaging, folding carton and corrugated board industries.
Founded in 1890 by Joseph Bobst in Lausanne, Switzerland, BOBST has a presence in more than 50 countries, runs 19 production facilities in 11 countries and employs more than 5 600 people around the world. The firm recorded a consolidated turnover of CHF 1.372 billion for the year ended December 31, 2020.
Press contact:
Gudrun Alex
BOBST PR Representative
Tel.: +49 211 58 58 66 66
Mobile: +49 160 48 41 439
Email: gudrun.alex@bobst.com
Follow us:
Facebook: www.bobst.com/facebook
LinkedIn: www.bobst.com/linkedin
Twitter: @BOBSTglobal www.bobst.com/twitter
YouTube: www.bobst.com/youtube
PR_BOBST_I.B.E. success story_14-10-2021_EG.docx
DOCX 66 KB
The release (available in English, German, French, Italian, Spanish, Portuguese and Russian) and images are available for download at https://dam.bobst.com/Go/vDzxCQT2.